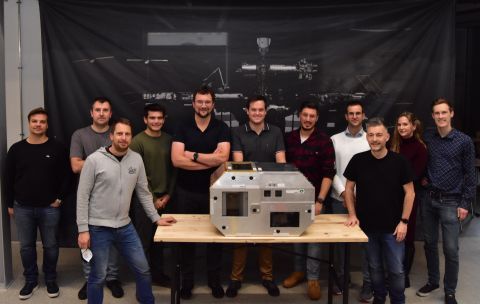
Flawless Photonics settled in Luxembourg in 2021 and specializes in manufacturing optical glasses, fibres, and components in microgravity. The company produces the so-called Space FiberTM, an optical fibre from a fluoride glass called ZBLAN, produced in microgravity conditions in Low Earth Orbit (LEO).
Flawless Photonics recently started producing fibre using ZBLAN onboard the International Space Station (ISS) resulting in the production of almost 12 kms of high-quality fibre in space. Building on its successful experiment, it is the first company to achieve such a feat in microgravity.
While the US headquarters focuses on the commercial applications of the fibre, the Luxembourg-based office focuses on the production side and counts 14 “machine builders” - from space engineers and robotics experts to chemists – who are actively working in close collaboration with NASA and the European Space Agency (ESA) among others, to create a flawless fibre.
With a career spanning almost 15 years in the space sector, Hubert Moser is a Senior Director Engineering at Flawless Photonics and manages the Luxembourg office. Taking a step back, he is reflecting on the milestones and achievements his company and team have made so far.
Where did Flawless Photonics come from? Why did you settle in Luxembourg?
My colleagues from the US came to Luxembourg and saw great opportunities here. They saw the support that one can get as a company, as a startup and that was the rationale behind coming here.
Flawless Photonics started operations Luxembourg in 2021 during the COVID lockdown. I was very much interested in building up a team and by in-space manufacturing which for me is the next step towards technology innovation and which, by bringing items back to Earth, has a direct value and contribution here on our planet.
Due to COVID, we started 100% online with online meeting and everybody was working from home. We then moved to the City Incubator and got a desk, a chair, and a meeting room. 3 months later, we moved into a small garage in Wecker and started building stuff and testing before moving to our current office 6 months later. None of us had worked with glass fibre before so we got into the topic and experimented a lot. We also started to work with NASA. The goal was always to produce glass in space and fibre with a better quality than what you could find on Earth. And we did quite a big step recently, also at a commercial scale.
Why glass fibre? And why microgravity?
During my studies, I had the chance to attend a lecture by an astronaut. It was about space stations and commercial usage on the ISS. The astronaut was saying that material science is one of the most promising areas to develop on the ISS and that using microgravity or the absence of buoyancy will be instrumental.
Somehow, the idea sticked and I got reminded of that potential when I got contacted to work for Flawless Photonics in Luxembourg.
By the way... the name of the company came from the promise of the glass which aims to be flawless. :)
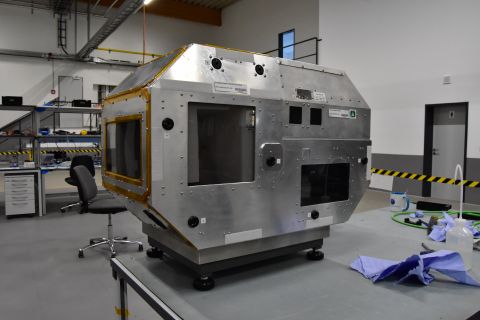
What are the benefits of having fibre glass produced in microgravity? Why does it make it more interesting?
The specific ZBLAN glass that we are using tends to crystalize incredibly fast compared to other types of glass. Many people want to have this glass, but it is very difficult to produce it at a very high quality, i.e. without crystals.
Microgravity removes the crystallization because it removes buoyancy and the movement of the glass ingredients which is the starting point for a crystal to grow. That is why microgravity is a key resource for us. The glass we produce in microgravity is 10 to 100 times more transparent than typical glass that you will find in your house.
The second big benefit is that this glass can transmit, compared to other glasses, a much wider spectrum of colours, from the deep ultraviolet to the long wave infrared. This means that there is a very broad spectrum of light and colours that you can send through that glass. You can use that to increase the amount of data that you can push through the fibre. The more colours you have in the spectrum, the more data you will be able to transfer simultaneously.
Drawing fibre with ZBLAN is also interesting because you can use it for lasers and sources of lights difficult to access. It is the case for the mid-infrared light which has a very specific spectrum of colours where lasers are currently limited by the glass quality. ZBLAN is one the few materials that have such a wide spectrum of colours that you can actually use for mid-infrared lights.
Another aspect is that 80% of our global communications are still going through cables and it will probably stay as it is. Even if satellite communication is increasing in terms of connectivity, today the overall ratio is 80% cables and 20% satellite communication, and it is highly likely that this will pretty much stay the same. Satellite communication will serve rural or underserved areas where cables are hard to lay down. But the backbone of the Internet will remain cable based.
On another hand, the World’s data hunger is always increasing. UH4K video on the phone, 4K video streaming increasing to 8K… the amount of data we consume is tripling every two years. This is why ZBLAN is considered as one of the most promising materials that will eventually replace existing cables.
How does this trend serve your business model?
Two types of fibre are currently available worldwide: the long format fibre which is over 50 kms long and the short format fibre, which is what we are doing now at Flawless Photonics, in a kilometre range.
The short format fibre, which is currently our short-term business, can help industries with light sources in different wavelengths and amplifiers or even with lasers needed for applications outside of the telecom industry such as for medicine or material manufacturing.
The long format fibre is useful for long-distance applications but to be able to produce it, we will need to scale up and to make another step towards technology development.
Right now, the length of our fibres is determined by our raw material, so-called preforms. If we want to go to regions where we will have to draw 50, 100 or 1000 kilometres of fibre, either the preforms will have to grow massively or we will have to change the process of drawing fibre to melt it up and draw it right from a molten state.
This is one of the technologies we have started working on. But this will require some time as there is still some technological work to be done until we can produce long format fibre.
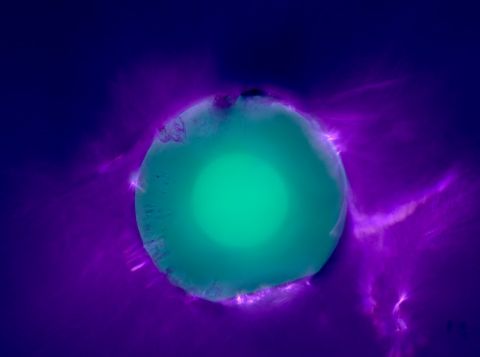
What is a preform and what does it look like?
It is 10 centimetres long and looks like a hot glue stick. A preform is composed of at least two layers of glass. In the middle, you can find a core glass and on the outside a cladding glass. These guide the light so that it does not fade and is guided through the fibre or preform. Then, the fibre drawer stretches this 10-millimetre diameter preform until it reaches the diameter of a hair.
If you want to produce long format fibre, will its characteristics be affected compared to the short format fibre?
In principle, no. Although right now we're producing 5 distinct types of fibre in space. One of them is the type that we will need for telecommunications, transmitting data. There are a few other types that are more for lasers as they are doped. If you send some light into them, they start to glow in a different colour and emit that light lase. So, there are different types of fibre, but the overall characteristics of the glass itself remain the same.
You mentioned there is still some technological work to be done on the long format fibre, can you explain?
There are actually two things to achieve this. The first one is to have the best glass quality possible. The second one is to improve our preforms, our raw material. We have been working on the preforms with partners in Poland and Australia like the Universities in Warsaw and Adelaide, and we believe we can further improve the quality of those preforms, so we have started experimenting on it about a year ago together. One of the next machines we would like to send to the ISS would be a preform maker to start making preforms in microgravity.
Does microgravity have an impact on the quality of preforms?
Yes. Crystals form while making preforms and when they are formed, you cannot get rid of them anymore. This means they will still be present in the fibre made from these preforms and reduce the quality of the fibre.
But we found out that if the preforms are manufactured in microgravity, the number of crystals will be negligible. Our research team in the US, working with Lawrence Livermore National Laboratory, created a number of simulations modelling the entire life of the glass in its different shapes strongly indicating that a large portion - more than 50% - of the transparency improvement comes from making the preforms in microgravity.
So, if we take your methodology and compare it to producing preforms and glass fibre on Earth in a more traditional way, is there a real competitive advantage in doing it in microgravity? The price of sending everything to space, producing fibre there - even though the launch price has been decreasing and becomes more accessible now - is still very expensive. So, what’s the real deal here?
On the price, we are paying the glass we are sending to the ISS per kilogramme, and we are selling our fibre per metre. From 50 grammes of glass, we roughly get 1 kilometre of fibre. So, it's a real advantage to produce and offer a larger quantity of fibre to our customers than the raw quantity of material we send out to space.
In terms of competitive advantage, they are basically 3 competitors worldwide who do fibre drawing and glass making terrestrially and most of them do it manually. What we did is we automated the process drastically which also reduces the production cost of that fibre here on Earth.
With the drawing tower we used in the beginning, we were told that fibre drawing is an art and when we started, it was really a little bit like you shouldn't drink a coffee before you start drawing a fibre. It's a very manual process, hard to repeat, hard to control. And we realized we needed to change the process because we had to go to space, and you cannot have an astronaut doing “art in space” for you all the time. So, we automated that process.
The trickiest part is starting the draw. This is where our competitive advantage comes in over our competitors who have done that or try to do that in space because they didn’t have the capability to initiate automatically and restart the process in case the fibre breaks. So, both on Earth and in space, this is one of our key advantages.
Does it mean that you could consider using your technology to produce, lower quality glass fibre for other uses on Earth as well?
Yes. That is also part of our strategy to enter the market. We are now working with potential customers who don’t require the best fibre quality but would like to test what we offer. We have started working with those potential customers to give them the fibre we produced here on Earth with the big draw tower, but also with our small machine that we have here on the ground.
We actually have 2 similar machines. One of them is on the ISS, the other one here is our engineering model which is more or less a replica with a little bit more holes and more tape on it. But it works the same and we are still drawing fibre here with that small machine. It also serves to compare the fibre to the one we draw in space.
What were the main hurdles you faced in the project?
There were a few hurdles when we went through the process with NASA in getting accepted to operate in the ISS. That was quite a thing, and we got some surprises. For instance, we had to do some testing for NASA and the post-analysis of the test results turned out to be much longer than expected. We just didn't know this would take such a long time and that task was on a critical path. ESA really helped us there. We finally performed the tests here in Luxembourg and sent the data earlier so that the analysis of the results could start at an early stage.
Additionally, we were also nicely surprised when we had to do our Preliminary Design Review (PDR) at ESA, and we were wondering how we could test our machine before going to the US for the official test where all interfaces are checked. It turns out that they have a functional model of the microgravity science glove box in the archives of ESTEC, which is the exact same box where our machine is installed on the ISS. We were finally allowed to perform a very early test of our machine using realistic conditions, without microgravity, which allowed us to start earlier with the production of our flight model. That removed the potential hurdle to find out that the machine wouldn’t fit inside the box, and it turned out that we were one of the few ones that didn’t have to go back and rework the machine. It was very helpful that we could test it upfront in Europe.
Another hurdle we had to face was about operations on the ISS that were sometimes stressful because of safety control measures. Some safety issues already occurred in the past as fibre has been known to float in the ISS. In this case, it is important to note that this can have a huge impact on operations like preventing astronauts from entering the module in which the fibre is floating for a given period for instance. So, we wanted to avoid that situation to happen.
A very good and funny example during our operations was that one of our favourite astronauts Loral O'Hara, who was on the ISS at the time of our experiment, had very curly hair. Sometimes we couldn't even see our machine with the ISS cameras when she had her hair open. As you know, optical fibre is approximately the same diameter as a strand of hair. One day, as she closed the machine and flew away, her colleague, Andy Mogensen had to work on the machine the following day. Before he opened the machine, he saw something flying around, and he got super scared. He thought there was fibre floating in the ISS. He took it, pulled it and saw that it was a hair, a hair from Loral!
That was a tense and tricky period, and it went on until we started operations on the ISS. Lots of people were scared about fibre in the ISS, but after our second run, they saw that what we were doing was appropriate and that we were not jeopardising any crew.
We had to discuss a lot with the safety panel at NASA before flying to the ISS to verify that everything was fine on our side. We had to rework a little bit our machines, but luckily, we had already foreseen one of the systems which became quite important later as it serves as an internal cleaning system that increases the safety of astronauts when they open the machine and operate it.
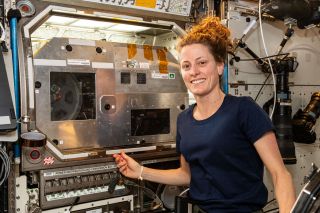
What would be the lessons learned for other companies willing to do in space manufacturing or work with partners like NASA for example?
For in space manufacturing, particularly on the ISS, I would say that we started a little late with the whole safety and integration work, which was, on one hand, a good thing because we already had a machine that had been tested. On the other hand, we had to rework it several times because the requirements changed during the process and as we were late, we had to adapt a lot each time. I can say that now, with the second machine, we have started the process much earlier. We will rather stretch the schedule than delay its start and involve safety much earlier. It is important to tell your stakeholders what you have in mind so you can also get their position. So, I would really advise others working on the ISS to start early in the process and make sure you have all the elements.
Moreover, the reviews we had with ESA were also very helpful because we learned many things we were not aware of, and they got to know what we were doing. They were very supportive and enabled us to perform early-stage testing. A little later we had to do some sound engineering of our machine and they were like “hey, we have this sound metre, do you need it?” so asking ESA for help was super helpful.
Beyond the reviews, they also helped us with reaching out to an independent body and getting feedback. That was very helpful because sometimes you’re such in your tunnel that you may oversee things and an external review is much needed. They also pushed us to get an additional safety measure that was not needed initially, but after another project’s fibre accident, became necessary, so we were lucky to have it.
What are the next steps for Flawless Photonics?
We’re doing 3 things in parallel. The first one is preparing for a resupply mission, hopefully at the end of 2024, so that we can have another run sent to the ISS with raw material and spools.
The second one is analysing the fibre that recently came back from the ISS. This demands some efforts like identifying pieces we want to analyse and the people who will analyse those pieces. We are working there with the Warsaw University, the University of Adelaide, ESA and the Danish Technical University. We are also selling selected pieces of fibres to early customers. We will also need to produce some fibre here for comparison.
The third part is the preform making machine which will hopefully bring us to the next step with much better transparency and performance than the current fibre produced on the ISS.
Talking about analysing the fibre which recently came back to Earth, how much have you produced now and how long is it?
Almost 12 kilometres. 11.9 to be correct. But we won’t analyse 12 kilometres of fibre. We are going to take some samples from each piece of fibre. We have diverse types of fibre as well and we will send some pieces to our early customers and partners with whom we worked already. Another partner came recently and said they want to see if and how they can use our fibre even if it doesn’t reach the best quality yet. And there is also a part of the fibre we want to use ourselves to make a laser to be used as a testbed. We are currently sorting all this out. It is a little coordination effort, but it is a good effort to make.
Is there anything you are hoping for?
I hope that we will see a good improvement with the fibres that we will be analysing in terms of quality, like strength. And then, the other hope is to get through this preform maker project and make it even faster than the current fibre maker we have because we will then be very close to having a flawless fibre.
We are now in the early prototyping state for the preform maker. It takes more time as melting glass is a bit more advanced in terms of challenges than drawing glass. The current launch date for the first preform maker to be sent to space is summer 2025.
In the meantime, we hope we will be able to make some preforms here on Earth and send them up in our resupply mission to be drawn with our fibre maker. That would be the ideal scenario as that would mean the preform maker would have proven that it can do things that others were unable to do on Earth so far.