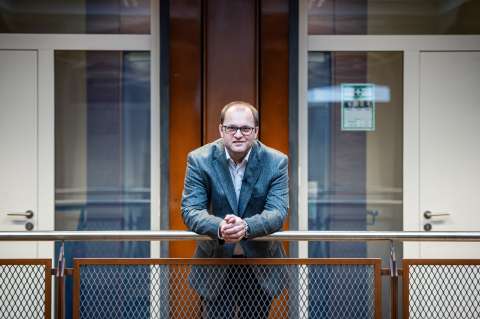
Gradel has worked in the nuclear industry for 50 years and for the last decade the company has also been involved in the space industry, constructing highest end mechanical ground support equipment.
In the last year and a half Gradel has been working with the German company, AMC. They’re specialists in ultra-lightweight construction and collaborate with Gradel to develop ultra-lightweight materials for the space market.
Obviously, weight is important for the space industry. But how important is it exactly?
In the launching business alone, lightweight construction has a lot to contribute. Today we have launch prices of about €5,000 per kilo to low orbit. So, each kilo, or each gram we save, will either have a noticeable effect on the cost of satellites and thus on the end user price, or the benefit could be used for increasing the payload of the satellite.
Who are some of your clients?
We provide equipment to customers including Thales, Airbus, and OHB. We look for customers in other parts of the world as well. In Europe most of our devices are needed in programs of The European Space Agency.
We have recently developed automated equipment like a smart multipurpose trolley used to move large satellites around in a clean room, self-leveling lifting devices and antenna support structures.
Safety factors are an important design factor, but it's also important to meet mass requirements, combined with, small deformation, or high stiffness requirements that we work with. These push us more and more to use innovative materials.

Are there any specific projects you can talk about?
Right now, we have an exciting R&D project in the works, qualifying AMC’s extremely lightweight materials technology, xFK in 3D, for use in space.
This means we have to test for extreme temperature gradients, going all the way from 180 °C to minus 180 °C as well as outgassing topics. There are some extreme vibrations during the launch of the satellites and so we need to deal with those too.
In combination, these problems can be quite challenging. Doubly so because the technology behind xFK in 3D is not known in the space industry as it’s very new.
How exactly can this product be used in space?
xFK in 3D would be used to make brackets. This is just the general term for making the link between two interfaces, which need to be fixed together for transmitting a given load case.
We are able to integrate other functions, such as vibration damping, into our brackets, which is not possible with metallic components.
Our brackets can be used for optical benches too. These need a very high precision. We’re talking in terms of flatness of 15 to 20 micrometers.
At the SpaceTech expo in Bremen, you showed a bracket of 280 grams which can hold 10 tons. How does that work?
We are using high efficiency carbon fibers. These are extremely stiff and we are only laying them in areas of the structure where they are needed. So ‘structure follows force.’ In between we have just air.
This gives us highest resistance components and, as carbon is much lighter compared to metal, we are at least 50% but very often much lighter.
That enables us to create a bracket of 280 grams which can handle almost 10 tones. It’s amazing.
This also shows that products developed for space can have real benefits here on Earth.
It's certainly true in this case. xFK started on Earth, in the automotive market and for sports. Now, aeronautics are very interested in it and space as well, but it started in automotive.
You’re holding the Lightweight Symposium on 7th of February, here in Luxembourg. Do you have a detailed program yet?
The highlight of the event is the market and technology study we completed last year, entitled ‘Space 2020 - Winning strategies for innovative lightweight solutions.’
In creating this report we had 43 partners, from nine countries and it's all about lightweight materials used in space.
I'm personally convinced that lightweight in general will be of great interest for the next few decades of the space industry, as well as other fields.
And the rest of the show?
There’s lots of speakers too, experts in lightweight construction, space, aeronautics, automotive and even a famous racing car driver giving its impression about the importance of lightweight for racing cars.
In fact, we also have an exhibition of some interesting lightweight products. In particular, a 575 kG race car which set a number of track records in Germany as well as the ultra-lightweight seat which won the German innovation award and the Altair enlighten award 2019. It’s going to be an exciting day for anyone interested in high end lightweight applications.